THE MASTER OF CRAFT
THE MAIWAI SPIRIT
KAMOGAWA, JAPAN
Scroll to explore
The Story
A CONVERSATION WITH KOSUKE AND RIKI SUZUKI
MAIWAI CRAFTSMEN IN KAMOGAWA, JAPAN
Kosuke Suzuki is a Japanese maiwai master teaching his son, Riki, the craftsmanship skills necessary to continue the two hundred year old tradition of ceremonial garment making. The hand-painted and hand-sewn kimono and hanten jackets made in their Kamogawa atelier are meticulously crafted by applying methods honed through years of observation and deliberate practice.
I strive every day
KOSUKE SUZUKI, MAIWAI MASTER
to create something
that pleases me.

S+O — HOW DID THE TRADITION OF THE MAIWAI BEGIN?
K. Suzuki — Originally, maiwai was a celebration for fishermen when there was a large catch. They would celebrate amongst themselves the fortune of this catch and, as part of the celebration, there would be a specific kimono that was handed out. Eventually the kimono itself started to be called maiwai.
S+O — WHAT ARE THE CHARACTERISTICS OF A MAIWAI?
K. Suzuki — A maiwai isn't really a kimono in the traditional sense. The customary women’s kimono is made of silk. For maiwai, the material is cotton, so it's more humble but, at the same time, extremely loud. You could say that it is formal wear made for a fisherman. When you wear this out to a festival, you want to stand out from the crowd. The scenes drawn on the design, depict the fisherman’s most common catch, or involve imagery of auspicious symbols like a crane or a tortoise, or portray folklore stories like the seven lucky gods or the sea goddess Otohime of the Ryugu kingdom. There is also the hanten style which is shorter than the kimono and includes similar patterns without the kimono sleeves.


S+O — WHEN DID YOUR FAMILY BEGIN CREATING MAIWAI AND HOW DID YOU DECIDE TO FOLLOW THE TRADITION?
K. Suzuki — Our family has been in the trade for over ninety years now. We started in 1925. As a child, I always watched my father working. When I was twenty-two years old and straight out of university, I was looking for work elsewhere, but there weren’t any opportunities available due to the 1970s oil crisis. Working here came naturally to me since I had been familiar with the work process and flow ever since I was a little kid.
R. Suzuki — When I was younger, I didn't really have any intention of continuing the family business. I knew how difficult the work was, and I didn't find it appealing. But, when I was older and thinking about my job prospects, I happened to see my grandfather's work displayed in Monterey, California. This was in the midst of my personal turmoil, when I was really contemplating what I was meant to do with my life. It turns out that this was the work I was meant to do, where I could actually leave something meaningful behind.
S+O — WHAT IS THE FIRST STEP IN THE CREATION OF A MAIWAI?
K. Suzuki — First, we start with the design. The imagery is very important. The design is drafted onto three layers of washi paper and then hand-carved into a pattern. Some of the patterns are nearly one hundred years old, others are new. This process takes a long time as we have to be careful when thinking about the placement of the design, and the color combinations that will work best with the imagery.
R. Suzuki — We start with a rough draft of the design before transferring the drawing onto the washi paper. After that, we carve the drawing using a kogatana [small knife]. Since the garments are custom made, the clothing pattern is based on the customer’s measurements. Once we have the clothing pattern ready, we decide where to place each drawing on the cloth. Then, the dyeing process begins.


S+O — WHAT ARE THE STEPS TAKEN FOR THE DYEING PROCESS?
K. Suzuki — The first thing is to transfer the design to the cloth using a soy-based glue substitute. We spread the glue all over the pattern, and apply it evenly to the cloth on the carved sections. The pressure must be exact when doing this. I still do most of the placement as my son is still learning this step. Then, we generally use pigment paints for our work as they are less likely to fade in the sun and saltwater than the dyes made for traditional silk kimonos. We take a lot of time to prepare the desired pigments and, only when they are ready, we begin painting the design. There are specific steps that need to be taken to seal the design using soy glosses. When it’s fully dried, we can then dye the whole garment in indigo. It’s a long process. Finishing a piece in a month is impossible. It takes two, maybe three months to create a garment.



Finishing a piece
KOSUKE SUZUKI, MAIWAI MASTER
in a month is impossible.
It takes two, maybe three
months to create
a garment.
S+O — HOW LONG DOES IT TAKE TO MASTER THESE TECHNIQUES?
K. Suzuki — I'm sure that every craftsman faces many challenges. Even after forty years, I still have times when I'm not satisfied with the quality of my work and it doesn't turn out the way I want it to. I think every day I strive to create something that pleases me. I wasn’t taught these skills step by step. Back in the day, you learned by watching. I would watch and then try something on my own. This meant that I failed many, many times. But I learned from my mistakes. I would always try to create what I envisioned. This meant that I learned by mostly teaching myself.
R. Suzuki — I just started learning this craft five years ago. I would watch my father and then try to practice the steps myself. It’s all mimicry. When I first started, I couldn't really perform well most of the steps, so I preferred painting the colors on the designs since that was what I was best at. Now though, I like to draw myself. I can't do anything big yet, but I'm finally able to also carve the stencils out. I really like the carving, the drafting, and the designing.

S+O — HOW HAS THE RELEVANCE OF THE MAIWAI CHANGED OVER TIME?
K. Suzuki — Until the 1950s [Showa 30s Era], maiwai kimonos were always handed out as part of the celebration for fishermen. But soon the kimonos became outdated due to lifestyle changes. Fishermen preferred some kind of financial bonus, something common now, to this type of ceremonial garment as a reward. The tradition has remained, but it isn’t as popular as it once was. There used to be thirty to forty families here in the Chiba Prefecture involved in this trade. There used to be a variety of craftsmen who focused on one of the tasks, such as carving or coloring. Now we have to practice all of these skills on our own. Now there are only three families, that I know of, still performing the craft.
S+O — WHY IS IT IMPORTANT FOR THIS TRADITION TO CONTINUE?
R. Suzuki — I think it’s important because it is a tradition that was born here in Japan. Our traditions are very regional. Maiwai has been a part of our local culture since the Edo period. That’s two hundred years of history. I don’t know whether the other two families involved in the maiwai business have capable successors to continue the legacy. So if I don’t do it, the culture of maiwai itself will likely perish. This work requires a lot of effort and time to gain the necessary skills. Once the craftsmanship is lost, it would be difficult for someone to revive it. This is why I feel the urge to continue it.
K. Suzuki — To be honest, while I was excited that my son would continue the business, I was also really concerned about his future. Would he be able to support himself from this work solely? But we’ve been exploring alternatives where we are also hosting workshops, and creating hand-dyed items that can be used in everyday life to supplement the business. My hope is that we can create inspiring new pieces that can be sold alongside the maiwai garments so that we can survive financially.
S+O — WHAT INSPIRES YOU TO CONTINUE?
R. Suzuki — We create items that are memorable. We’ve had customers who have ordered more than one mawai kimonos, or others who have purchased our pieces as gifts. It brings me joy to hear that someone received our work and liked it so much that they had to buy another garment and offer it to someone they care about.
It turns out this was
RIKI SUZUKI, MAIWAI APPRENTICE
the work I was meant to do,
where I could actually leave
something memorable
behind.
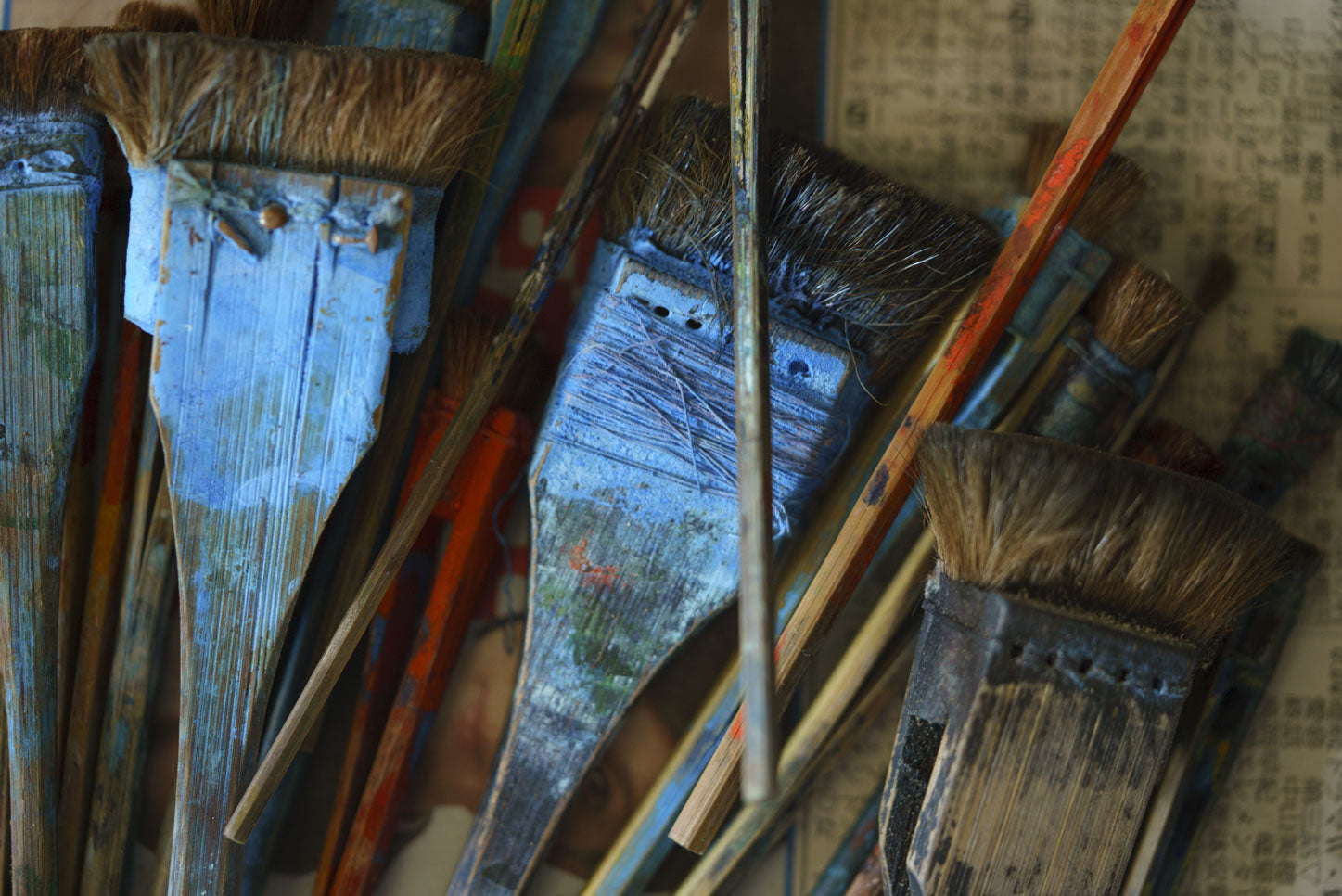
Credits
Photography by Brian Sokol
Film by Oresti Tsonopoulos and Alexandra Stewart
Special Acknowledgments - Shinichi Kinoshita and Miwa Okada of Fixers Japan
The Objects
Exclusive Edition 010 Japanese Maiwai Jacket
Maiwai has a two-hundred year history in the Japanese fisherman culture. This jacket, typically in a kimono or hanten style, was traditionally given to the fisherman as a reward for a bountiful catch. The hand-crafted jacket takes between two to three months to create with meticulous detailing from hand-painting, indigo dying and sewing.
The Destination
KAMOGAWA, JAPAN
The town of Kamogawa lies within the Chiba Prefecture just a two-hour train ride south of Tokyo on the Pacific Coast. The town is mostly known as a laid back fishing suburb, and home to a popular marine aquarium park. A visit to Kamogawa can easily be enjoyed as a day trip from Tokyo when one needs a break from the pulsating city and a moment to relax in an unfussy seaside setting with fresh, salted air, and perhaps partake in the budding surf scene.